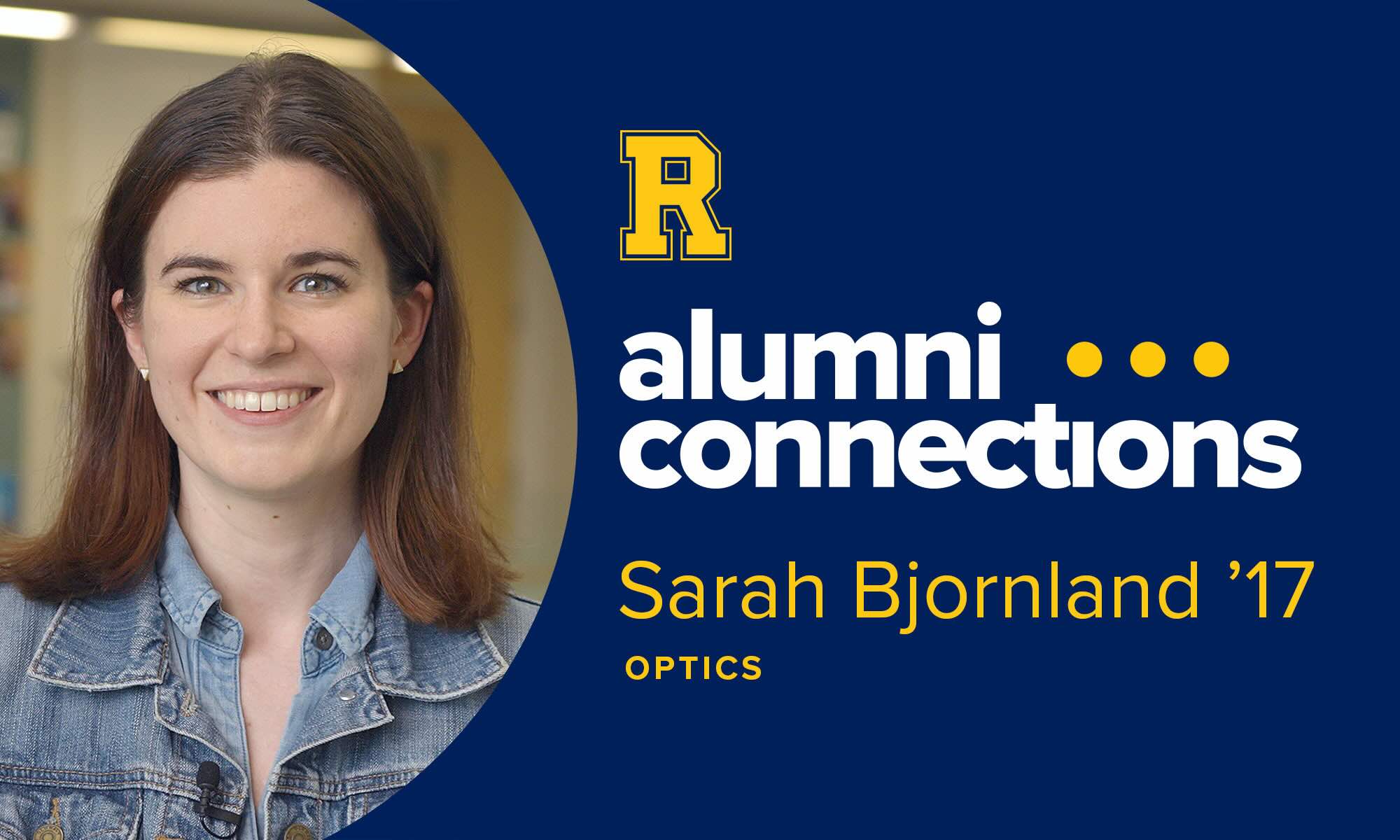
Campus Life
Sarah Bjornland ’17: Embracing her management superpowers
Meaningful connections with faculty and industry experts helped the Rochester graduate find her niche in the field of optics.
Rochester researchers on the growing concern of plastics exposure on human health.